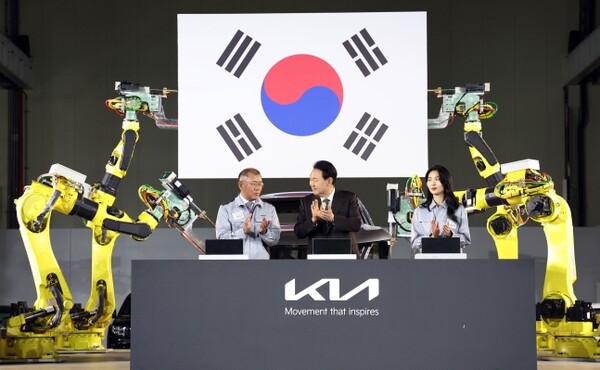
[NewsSpace=JeongYoung Kim] Hyundai Motor Group has started building a new domestic car factory in Hwaseong, Gyeonggi Province, on the 11th of April, after a 29-year hiatus of not constructing any new plants in South Korea. The factory will be the first electric vehicle-only factory in the country and the world's first PBV(Purpose Built Vehicle) factory. PBVs refer to vehicles that are tailored to various business needs, such as delivery vans or mobile offices. They are receiving attention as vehicles that can respond to various demands in the era of electric cars. The company plans to invest 1 trillion won in a 30,000 square meter site at the Kia Hwaseong plant and produce 150,000 vehicles annually from the second half of 2025.
Hyundai Motor Group plans to use this factory, along with other domestic production facilities, as a key hub in the global competition for electric vehicles. They have set a goal of producing 1.51 million of the 3.64 million electric vehicles they plan to produce by 2030 domestically. They will also expand their current lineup of 12 electric vehicle models to 31 by 2030. To achieve this goal, they will build a new electric vehicle factory at their Ulsan plant later this year, and they are actively converting existing internal combustion engine production lines into electric vehicle production lines.
For the past 29 years, Hyundai and Kia have not built any new factories in Korea, but have established 16 factories in 10 countries overseas. The last time they built a factory in Korea was in 1997, when their domestic production was 1.85 million units per year. Since then, production has increased to 6.79 million units per year, including 3.19 million units in Korea and 3.6 million units overseas as of last year. Considering that about 4,000 people work at Hyundai's Asan factory, which produces 300,000 units per year, about 50,000 jobs were created overseas during this period.
Within the group, building new factories in Korea was once considered a kind of taboo until a few years ago. There were labor unions that went on strike and stopped factories for reasons that were difficult to understand, and Hyundai's average annual salary per employee was close to 100 million won(KRW), making price competition difficult. The domestic market, where the population began to decline, showed its limits.
Infrastructure-equipped domestic manufacturing capabilities are advantageous for electric vehicles... A stepping stone for the top 3 electric vehicle companies
The environment hasn't changed much, but what led Hyundai Motor Group to decide on building a domestic factory was the fact that electric vehicles, which are becoming more like IT devices, are high-value advanced products. They believed that the accumulated manufacturing capabilities in the domestic market for decades were essential to become one of the top 3 electric vehicle companies in the world.
One of the most important things to consider when choosing a location for a complete car factory is how to source parts. Hyundai-Kia reportedly considered the domestic market to be the most optimal choice, as there are hundreds of cooperative suppliers with whom they have worked together for a long time. After introducing hybrid cars in 2009, Hyundai has accumulated technical expertise and experience in the electric motor field for more than 10 years. They also believed that the electric vehicle-related manufacturing technology of the cooperative suppliers who participated in this process has reached a level close to the global standard.
In addition, the fact that electric vehicles are high-value products with advanced technology applied also had an impact. In the past, it was said that Hyundai-Kia had no problem with production if they only had a few parts suppliers related to the engine and transmission, which are core parts of internal combustion engine cars, when expanding overseas. They said that local procurement of the remaining parts, which did not require special technology, was sufficient. However, most electric vehicle parts are closely related to each other electronically, making it difficult to use the same local procurement strategy as internal combustion engine cars.
With the success of the Ioniq, Hyundai plans to produce 1.51 million electric vehicles domestically by 2030.
One advantage for Hyundai is the existence of domestic battery manufacturing companies, such as LG Energy Solution, that have world-class competitiveness. Collaborating with these companies can create synergy in various ways. Additionally, batteries are a critical component in electric vehicles, accounting for approximately 40% of the total cost, and foreign car manufacturers are risking their lives to collaborate with battery companies. Moreover, Hyundai's Ioniq and EV6, which were developed and produced domestically, have been popular overseas and have received numerous awards, demonstrating Hyundai's successful experience. Compared to internal combustion engine vehicles, electric vehicles have less price competition pressure, as their unit price is higher. Another advantage is that Hyundai and Kia have already secured export destinations for their electric vehicles, making domestic production more advantageous.
However, there are still many challenges, such as establishing good relationships with labor unions to ensure smooth electrification, and finding and developing competitive domestic suppliers to support electric vehicle production. Professor Lee Ho-keun of Daeduk University's Future Automotive Engineering Department said, "Following the establishment of the first electric vehicle plant, we need to accelerate the localization of electric vehicle components."